Resources
Jump to Section
No Minimum Orders
QTY 1-250,000
Injection Molded Plastic Parts
In 14 Days
100’s of Material Options
Custom Ordering
The Process:
Rapid Tooling (Class 103 Tools)
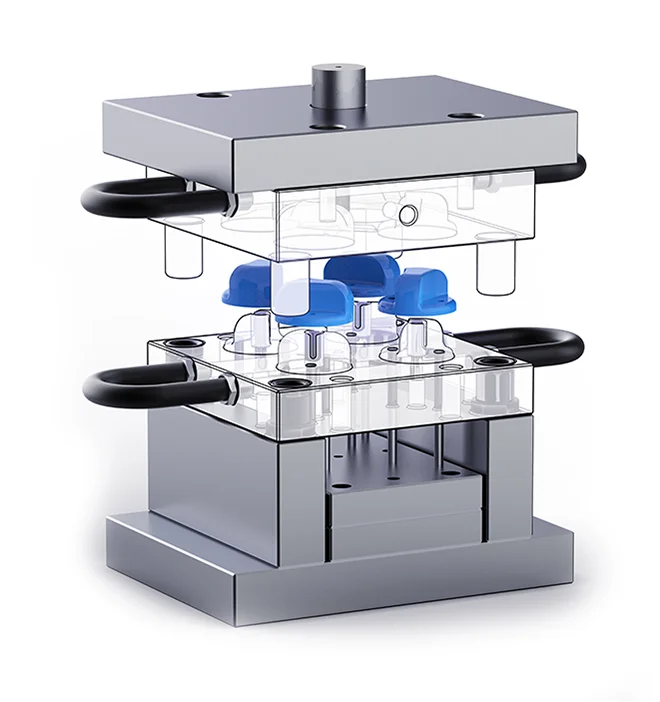
Short to Mid-Run Manufacturing
Additive Manufacturing LLCs enhanced
Rapid Tooling offers tailor-made prototype
and production solutions. delivering parts in
as little as 14 days. Our modular injection
molds provide design flexibility, allowing
changes in just days. These tools come at a
fraction of the cost of traditional production
tooling, yet yield the same high-quality
results, and are scalable for bridge tooling
and short-run production.
Cost-Efficiency and Flexibility
Class 103 inserts offer a cost-effective alternative to their higher-class counterparts, requiring no minimum orders and offering significant cost savings. The ability to produce these tools at a fraction of the cost of Class 102 or 101 tooling opens up new opportunities for manufacturers, particularly small to medium-sized enterprises. This allows our customers to access high-quality tooling solutions without breaking the bank. Additionally, the versatility of Class 103 inserts allows for a wide range of part sizes, from small components to large parts.
Steel Inserts for Superior Performance
With Class 103 inserts, steel is the material of choice for the inserts due to its exceptional durability, wear resistance, and thermal stability. Steel inserts provide superior performance over aluminum alternatives, offering greater longevity and reliability in demanding injection molding environments. The use of steel ensures that the inserts can withstand the rigors of high-pressure injection molding while maintaining dimensional accuracy over extended production runs.
Modular Design for Rapid Adaptation
A standout feature of Class 103 inserts is their modular design, which facilitates quick and cost-effective adaptation to design changes. The modular system allows for seamless modification of the tooling configuration to accommodate evolving project requirements. With the ability to make tooling modifications in just 1-2 days, manufacturers can respond swiftly to design revisions, optimize production efficiency, and minimize downtime.
Advantages
of Rapid Tooling
Thermoplastics: Real Materials
Thermoplastics are the most common materials in injection molding. Examples are Polyethylene (PE) / Polypropylene (PP) Acrylonitrile Butadiene Styrene (ABS) / Polycarbonate (PC) / Nylon (PA) / Polyvinyl Chloride (PVC)
Expert Support: DFM & Mold Flow Analysis
Additive Manufacturing LLC’s engineers review each project thoroughly. DFM analysis assesses part design, mold flow, materials usability, and tolerances, optimizing the tooling process for reliable and cost-effective production.
Rapid Deliveries: Molded Parts in 14 Days
Our Rapid Tooling delivers quality parts in as little as 14 days. By using modular inserts instead of creating full-scale molds, we significantly reduce lead times, reduce costs, and simplify design changes for greater flexibility and efficiency.
No Minimum Orders: Tailored to your needs
Whether you need a single prototype, a handful of parts, or a full production run, our tooling is tailored for quantities ranging from 1 to 250,000, providing solutions for both small and large-scale projects.
Production Finishes: Customizing Parts
Finishing options including mold texturing, polishing, threaded inserts, silk screening, pad printing, laser engraving, and assembly services. These capabilities ensure your parts are functional and tailored to your needs.
Seamlessly Transition: Prototype to Production
Once your prototype is perfected, modular steel inserts can be upgraded for higher-volume production. Our process allows production runs of up to 250,000 shots with enhanced durability.
Scaling
from Prototypes to Production
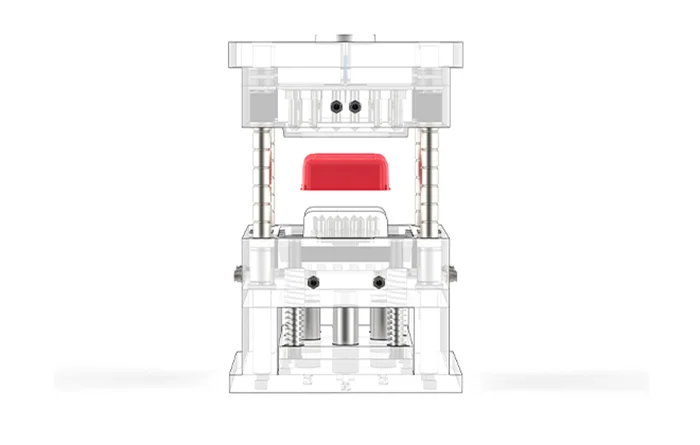
Rapid Tooling: Fast, Flexible, and Scalable Tooling Inserts
Additive Manufacturing LLC’s unique Rapid Tooling process focuses on creating custom steel inserts based on your CAD data, perfectly tailored to your part’s design. So instead of producing a full mold, we craft only the inserts, which fit into pre-made modular bases. This allows us to production-grade prototype parts in just a few days, drastically reducing lead times. Designed for low to mid-volume production, these inserts maintain the precision and durability of traditional molds while offering easy modifications for flexibility and scalability.
Seamlessly Transition from Prototype to Full Production
Our prototype tooling is designed with scalability in mind. Once your prototype is perfected, the same modular steel inserts can be enhanced for higher-volume production without the need for an entirely new mold. By simply upgrading the prototype tool for durability, our process enables production runs of up to 250,000 shots. This eliminates the typical downtime and costs associated with switching from prototyping to manufacturing. With our streamlined approach, you’ll move from concept to mass production faster and more efficiently, all while maintaining precision and quality throughout the process
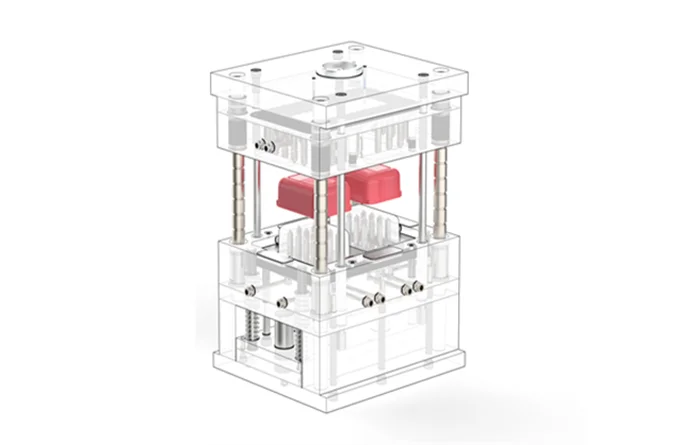
Rapid Tooling
Finishing Options
Injection Mold Finishing: Polishing
Achieve flawless finishes from high-gloss to matte with precision tool polishing. Improve part aesthetics, reduce defects, and ensure smooth ejection. Elevate your product quality with a polished surface that maintains tight tolerances and delivers exceptional results
Injection Mold Finishing: Textures
From sleek high-gloss to subtle matte, our textured finishes add style and function. Enhance grip, reduce glare, or conceal imperfections with precision. Achieve the perfect look and performance for your molded parts with our expert texturing options.
Injection Mold Finishing: 2nd Operations
Transform your injection-molded parts with our expert secondary operations. From custom painting and texturing to precision inserts and assembly, we add value and functionality. Elevate the look, fit, and performance of your products with our comprehensive finishing services
ISO 9001:2015:
Quality Systems
ISO Quality: ISO 9001 2015
Additive Manufacturing LLC is ISO 9001:2015 certified which ensures that our injection molding process and production parts will meet rigorous quality standards. We guarantees consistency, precision, and continual improvement, giving you reliable, high-quality parts every time. Trust in our certified commitment to delivering excellence.
First Article Inspection: FAI Included
First Article Inspection (FAI) verifies that the first part produced meets all design specifications and quality requirements. The FAI process ensures accuracy and consistency on every order, providing you with confidence that your injection molded part will match your exact standards.
Tolerances: ASTM Standards & GD&T
We adhere to the highest ASTM standards for tolerances in injection molding, achieving precision down to ±0.05 mm or even tighter when required. GD&T is also recognized and implemented in further ensuring part accuracy and repeatability, especially when performing FAIRs or producing parts that require PPAPs..
Domestic Inspection: Ensuring Results
Parts are shipped to our domestic advanced inspection facility in Las Vegas, Nevada where each component undergoes rigorous quality checks. Using precise measurement tools, including digital CMMs, we ensure every part meets our high standards before it reaches you, guaranteeing project success and consistency on every program.
CMM: Measurement Systems
CMM (Coordinate Measuring Machine) measurement systems provide precise, detailed inspections of your injection molded parts. Using advanced digital technology, they ensure every dimension is accurate and meets design specifications. This level of precision guarantees consistency and quality in every part we produce
Material Certifications: Certs Included
Material certifications guarantee that every component we produce meets strict quality and compliance standards. Material certifications provide full traceability and assurance that the materials used in your injection molded parts are consistent, reliable, and exactly what your project requires.
Thermoplastics
Materials
Thermoplastics: Real Materials
Prototyping and manufacturing using the same process and materials ensure the best results. This consistency guarantees that your prototypes accurately reflect the final product, reducing potential issues, and making the transition to production smooth and efficient.
Advanced Options: Specialty Blends
Thermoplastics or thermosets can be filled with various additives to enhance specific properties, like strength, rigidity, or flame resistance, & overall performance. Common fillers include Glass fibers / Carbon fibers / Mineral fillers
Elastomers: Flexible Parts
Elastomers- These materials have elastic properties, similar to rubber or silicone, and can be stretched significantly while returning to their original shape. Examples Thermoplastic Elastomers (TPE) Silicone Polyurethane (PU)
Recyclability: Reuse, Rebuild, Repeat
Thermoplastics can be melted and reshaped multiple times without significant degradation, making them highly recyclable. This property allows for reduced waste and the potential for reusing materials in different applications
Cost-Effective: Affordable, Modifiable, Reusable
Tooling with thermoplastics typically costs less than an equivalent small batch of printed parts. Steel inserts allow for rapid design modifications, providing optimal adaptability. Moreover, the tooling is reusable and can be repurposed for production, offering a flexible and cost-effective manufacturing solution.
Versatility: Tailored Design Solutions
Thermoplastics can be engineered to exhibit a wide range of properties. From flexible and elastic to rigid and strong, making them suitable for various applications across different industries, including automotive, consumer electronics, and medical devices where specific material characteristics are essential.
Semi-Crystalline
vs Amorphous
Semi Crystalline: Chemical Resistance, Heat Deflection
Semi-crystalline materials are the strong, silent types in plastics. They withstand harsh chemicals and high temperatures with ease. Their ordered molecular structure keeps them rock solid until they hit their precise melting point, making them ideal for tough, durable parts like automotive components and chemical containers
Pros:
- Chemical Resistance: They laugh in the face of harsh chemicals.
- High Heat Tolerance: They hold their shape and strength at high temperatures.
Cons:
- Injection Molding Challenge: Quickly turning from solid to liquid, warping issues
- Shrinkage: Materials shrink unevenly, which can complicate precision parts.
Amorphous: Precision & Consistent
Amorphous materials are the smooth operators of the plastic world. With their randomly ordered molecular structure, they gradually soften with heat, making them a dream to mold into precise shapes. They’re also isotropic, meaning they shrink uniformly and resist warping, and are perfect for creating sleek, dimensionally accurate parts.
Pros:
- Easy to Mold: They soften slowly, making them great for detailed, complex shapes.
- Aesthetic Appeal: They often have a superior optical clarity and finish.
Cons:
- Higher Cost: These materials tend to be more expensive.
- Heat Sensitivity: They lose strength quickly at higher temperatures.
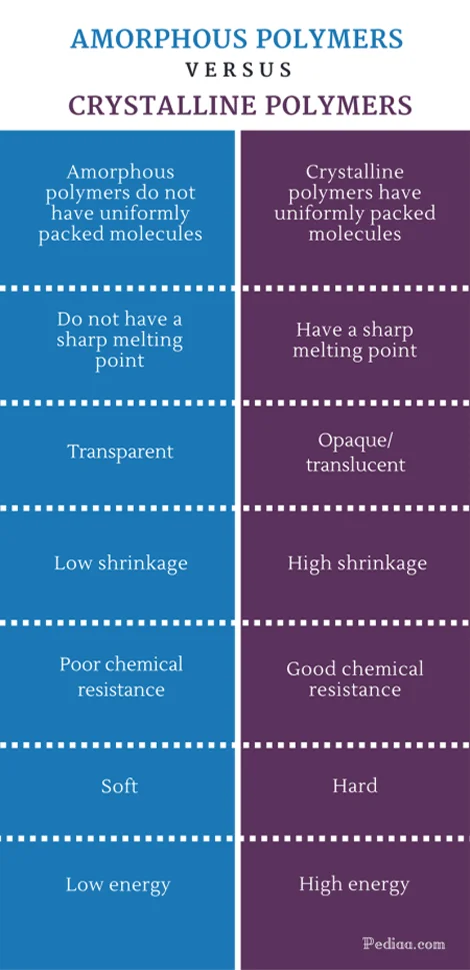
Amorphus
Thermoplastics
CELLULOSE ACETATE (CA)
Cellulose Acetate (CA) is a biodegradable thermoplastic known for its excellent optical clarity, impact resistance, and UV stability. It’s commonly used for eyeglass frames, packaging films, tool handles, due to its versatility
POLYVINYL CHLORIDE (PVC)
Polyvinyl Chloride (PVC) is a versatile, durable, chemical resistance plastic. PVC is also cost-effective and flame-resistant., making it ideal for pipes, window frames, and electrical insulation.
POLYSTYRENE (PS)
Polystyrene (PS) is an economical materials. Offering excellent clarity and rigidity, this material is suitable for a verity of applications, but is most commonly used to mfg packaging & disposable products
ACRYLONITRILE BUTADIENE
ABS, or acrylonitrile butadiene styrene, is a common thermoplastic polymer that is popular due to low cost and easy machinability. ABS has great impact and chemical resistance along with strength and stiffness.
ACRYLIC (PMMA)
Acrylic (PMMA) excellent optical clarity and weather resistance. Acrylic offers great transparency and rigidity. UV resistance and lightweight, making it ideal for signs, displays, and protective barriers.
POLYCARBONATE (PC)
Polycarbonate (PC) is valued for its strength and transparency. PC offers high impact resistance, heat resistance along with dimensional stability, and transparent options.
STYRENE ACRYLONITRILE (SAN)
Styrene Acrylonitrile (SAN) is known transparency, rigidity, & chemical resistance. Excellent dimensional stability and ease of process make it ideal for applications like kitchenware, cosmetic containers, and automotive parts.
POLYMETHYLPENTENE (PMP)
Polymethylpentene (PMP) is a lightweight thermoplastic known for its clarity, low density, and chemical resistance. It’s ideal for medical devices, laboratory equipment, and food containers due to its high temperature and impact resistance
POLYMETHYLPENTENE (PMP)
Polymethylpentene (PMP) is a lightweight thermoplastic with excellent clarity and chemical resistance. It’s ideal for medical devices, lab equipment, and food containers, offering transparency and high-temperature resistance
POLYETHERSULFONE (PES)
Polyethersulfone (PES) is a durable thermoplastic with high thermal stability and chemical resistance. Ideal for medical devices, filtration membranes, and aerospace applications due to its strength and transparency
POLYARYLATE (PAR)
Polyarylate (PAR) is known for its heat resistance, mechanical strength, and optical clarity. It is ideal for applications requiring toughness and transparency, such as automotive components, electrical housings, and lenses
POLYVINYLIDENE FLUORIDE
Polyvinylidene Fluoride (PVDF) is known for its excellent chemical resistance, thermal stability, and strength. Ideal for chemical processing, electrical insulation, and piping systems, PVDF also offers good UV resistance.
POLYPHENYLENE OXIDE (PPO)
Polystyrene (PS) is an economical materials. Offering excellent clarity and rigidity, this material is suitable for a verity of applications, but is most commonly used to mfg packaging & disposable products
POLYSULFONE (PSU)
Polysulfone (PSU) offers high-temperature resistance mechanical strength, excellent chemical resistance and dimensional stability, making it ideal for medical, automotive, and electrical components.
POLYTHERIMIDE (PEI)
Polyetherimide (PEI) is a high-performance thermoplastic with excellent thermal stability, mechanical strength, and flame retardancy. Ideal for aerospace and medical applications.
POLYIMIDE-IMIDE (PAI)
Polyamide-imide (PAI) is an ultra-high-performance thermoplastic known for its exceptional thermal stability, mechanical strength, and chemical resistance. Ideal for aerospace and automotive applications.
POLYETHERETHERKETONE (PEEK)
Polyetheretherketone (PEEK) is an ultra-high-performance thermoplastic known for its exceptional thermal resistance, mechanical strength, and chemical stability. It is ideal for aerospace, automotive, and medical applications.
POLYDICYCLOPENTADIENE
Polydicyclopentadiene (PDCPD) is a durable thermoset polymer known for its high impact resistance and chemical stability. It’s ideal for tough applications like automotive body panels, industrial equipment, and protective housing
POLYIMIDE (PI)
Polyimide (PI) is a high-performance plastic known for its exceptional thermal stability, mechanical strength, and chemical resistance. It’s ideal for electronics, aerospace, automotive’s extreme temperatures and harsh environments.
POLYIMIDE-IMIDE (PAI)
Polyamide-imide (PAI) is a high-performance thermoplastic known for its excellent thermal stability, mechanical strength, and chemical resistance. Ideal for aerospace and automotive applications requiring durability at high temperatures.
Semi Crystline
Thermoplastics
POLYAMIDE (PA) NYLON
Polyethylene (PE) is a semi-crystalline thermoplastic known for its excellent chemical resistance, flexibility, and impact strength. It’s commonly used in packaging, containers, piping, and household goods due to its versatility and durability.
POLYMETHYLPENTENE (PMP)
Polymethylpentene (PMP) is a lightweight thermoplastic known for its clarity, low density, and chemical resistance. It’s ideal for medical devices, laboratory equipment, and food containers due to its high temperature and impact resistance
POLYMETHYLPENTENE (PMP)
Polymethylpentene (PMP) is a lightweight thermoplastic with excellent clarity and chemical resistance. It’s ideal for medical devices, lab equipment, and food containers, offering transparency and high-temperature resistance
POLYETHERETHERKETONE (PPEK)
Polyetheretherketone (PEEK) is an ultra-high-performance thermoplastic known for its exceptional thermal resistance, mechanical strength, and chemical stability. It is ideal for aerospace, automotive, and medical applications.
POLYIMIDE (PI)
Polyimide (PI) is a high-performance plastic known for its exceptional thermal stability, mechanical strength, and chemical resistance. It’s ideal for electronics, aerospace, automotive’s extreme temperatures and harsh environments.
POLYETHYLENE (PE)
Polyethylene (PE) is a semi-crystalline thermoplastic known for its excellent chemical resistance, flexibility, and impact strength. It’s commonly used in packaging, containers, piping, and household goods due to its versatility and durability.
POLYMETHYLPENTENE (PMP)
Polymethylpentene (PMP) is a lightweight thermoplastic known for its clarity, low density, and chemical resistance. It’s ideal for medical devices, laboratory equipment, and food containers due to its high temperature and impact resistance
POLYVINYLIDENE FLUORIDE
Polyvinylidene Fluoride (PVDF) is known for its excellent chemical resistance, thermal stability, and strength. Ideal for chemical processing, electrical insulation, and piping systems, PVDF also offers good UV resistance.
POLYDICYCLOPENTADIENE
Polydicyclopentadiene (PDCPD) is a durable thermoset polymer known for its high impact resistance and chemical stability. It’s ideal for tough applications like automotive body panels, industrial equipment, and protective housing
POLYIMIDE-IMIDE (PAI)
Polyamide-imide (PAI) is a high-performance thermoplastic known for its excellent thermal stability, mechanical strength, and chemical resistance. Ideal for aerospace and automotive applications requiring durability at high temperatures.
Understanding
Injection Molding Tolerances
Influencing Tolerances: Injection Molding
Several factors influence the tolerances in injection molding, including material type, part design, mold design, and the molding process itself. Different materials have different shrinkage rates, which can affect the final dimensions of the part. The design of the part and mold also plays a significant role as complex geometries may require tighter tolerances to ensure proper fit and function.
Tolerances Variations: Across Materials
Thermoplastics have varying levels of tolerance ranges due to their unique material properties. Achieving the right tolerance minimizes the need for post-processing or adjustments, saving time and costs in the manufacturing process. Understanding and controlling tolerances in injection molding is key to producing high-quality, reliable parts. By considering factors such as material properties and part size, manufacturers can select the appropriate tolerance levels to meet their specific application requirements. This careful attention to detail helps ensure that the final product meets all functional and aesthetic standards.
Industry Standards: Tolerances
In the injection molding industry, tolerances are typically defined by standards such as those set by ASTM & GD&T. These recognizable standards provide guidelines for acceptable tolerances based on the part’s size, material, and intended use. For most standard injection molded parts, tolerances range from ±0.05 mm for smaller parts to ±0.3 mm for larger ones. High-precision applications may require even tighter tolerances.
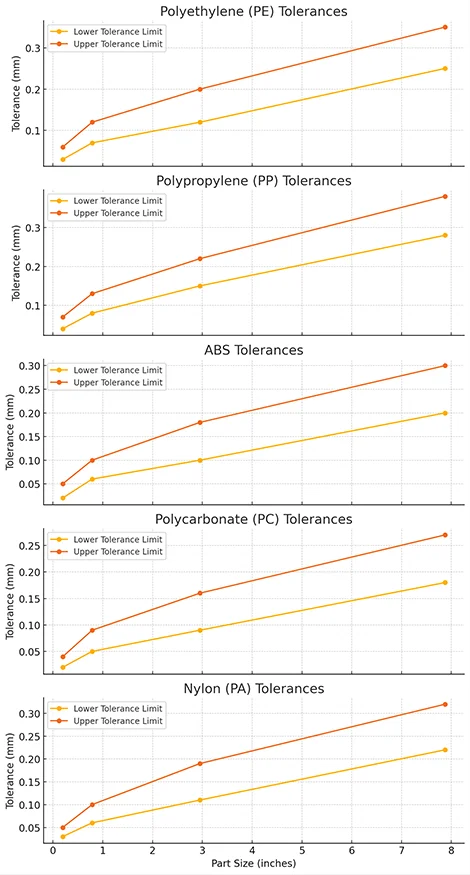
WHY CHOOSE ADDITIVE MANUFACTURING LLC?
ISO: 9001 2015 Quality Systems
At Additive Manufacturing LLC, our ISO 9001:2015 certifications is just the start. We go above and beyond with every project, including First Article Inspection Reports (FAIR) and Material Certifications for full traceability and quality. Our inspection facility uses advanced CMM technology, ensuring every part is crafted to perfection. We don’t just meet expectations—we exceed them. Choosing us means choosing precision, reliability, and a team dedicated to delivering parts that impress.
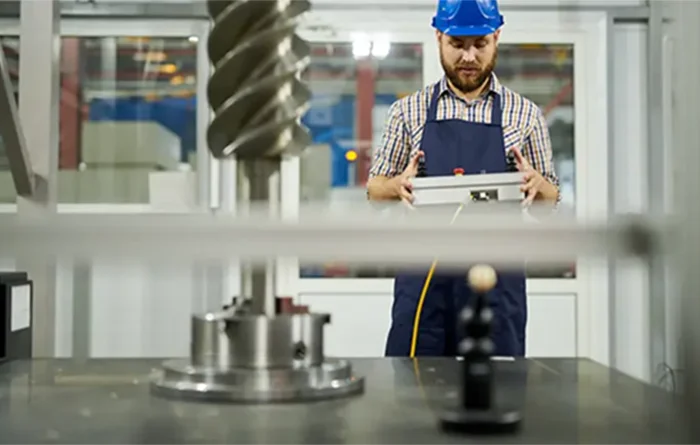
Experience: Legacy of Performance
With a century of combined experience in manufacturing, Additive Manufacturing LLC brings industry knowledge and exceptional customer service to every project. Our team of tooling engineers and project managers work meticulously to perfect your part, ensuring precision, communication and quality at every stage. We’re more than just a service provider; we’re your partners in innovation, and we are dedicated to exceeding expectations and building lasting relationships. Turn your ideas into reality with rapid tooling. Get a quote today and experience our commitment to excellence
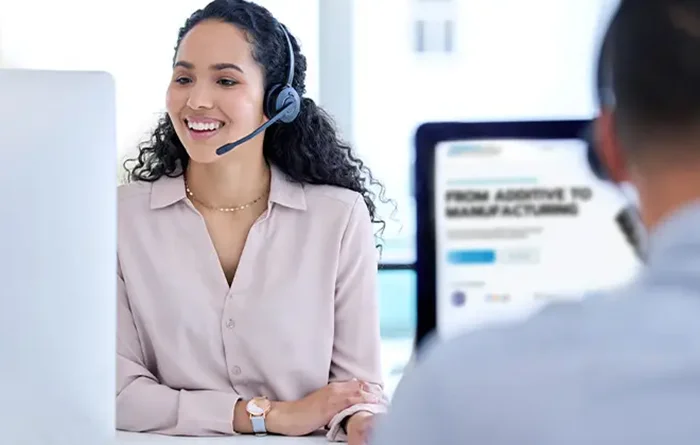
Expert Project Management
We don’t rush the swing, but we do make sure it’s precise. Our process combines the best of human expertise with cutting-edge AI to provide you with tailored quotes quickly and accurately. While we don’t do instant quotes, this method ensures each project is thoroughly evaluated and set up for success. We take the time to understand your needs, delivering a quote that’s right on target. With us, you’re getting more than just a number—you’re getting a partner for success.
Other Services:
No services foundGet in Touch with Us
Reach Out for Inquiries, Assistance, and More
Please contact us if you have any questions, comments or require
Need a Quote?
Features of our quoting system
Upload Files Directly
Just simply create an account, and upload your 3D files.
24 Hour Access
It can be hard to get things done over the phone, just use our system any time of day.
Digital Quotes
Upload your files, and we will send you a personalized quote.
Experienced Manufacturers
You can trust the brand Additive Manufacturing LLC
Best Prices
We offer competitive pricing to any client, small or large.
Register for your quote